« This new material has the molecular elasticity of a snail and the consistency of the train station of Perpignan »
In 1968, Jacques Daum meets with Salvador Dalí in Cadaquès, Spain, to suggest a collaboration in imagining sculptures in pâte de cristal (crystal paste, a unique proprietary technique by Daum. Dali, very interested by this prospect, declares: “Pâte de cristal is truly a Dalinian material. Hence I have used it to create masterpieces;I’m delighted by this new material, which has both the molecular elasticity of a snail and the consistency of the Perpignan train station”. Daum and Dali’s collaboration lasted over 20 years, and resulted in 28 artworks in pâte de cristal.
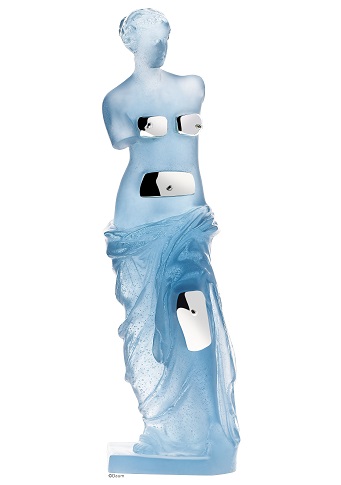
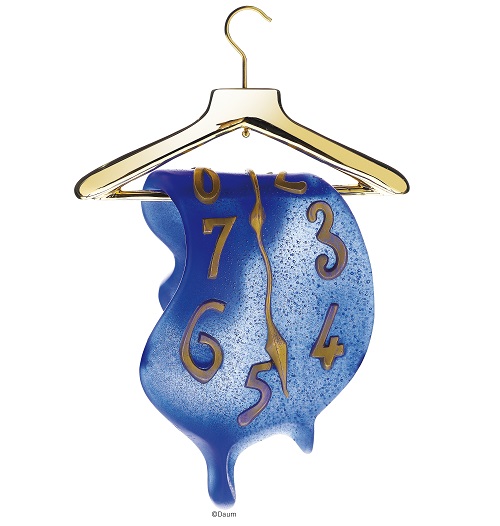
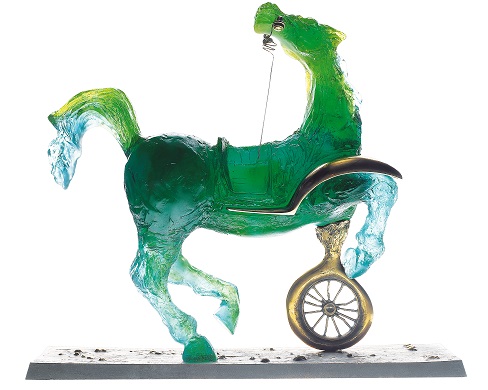
Manufacturing processes
1. Molding the model
The craftsman uses a sketch to make a first clay model. Volume, details and expressions are worked to perfection. Once the sculpture is finished, a negative mold is made out of elastomer.
2. Wax pouring
Hot wax is poured into the hollow mold after the original sculpture is removed.
3. Wax reproduction
When the wax has cooled and set, the model is removed from its elastomer mold.
4. A perfect reproduction thanks to the lost wax technique
The wax model is then chiseled and reworked by hand in order to obtain a perfect reproduction that is identical to the original. The wax model is immersed in refractory plaster. Under the effect of heat, the wax melts and drips from the plaster through previously made holes.
5. Filling the mold with pieces of crystal
When the wax cleared, the hollow part of the plaster mold is carefully filled with pieces of crystal of different colors and sizes. These pieces of crystal are also called groisil. Everything is then put into ovens at 1400° for many hours, depending from the size of the pieces.
6. Unmolding and finishing the sculpture
After cooling, the plaster mold is delicately broken, revealing the pâte de cristal sculpture.
7. Finishing and Signature
Quality control and color distribution takes place after finishing operations. The piece is then ready for the final touch: the Daum signature and the artist’s signature, depending on the case. The process is then repeated for each piece. Every work is unique.
Informations thanks to Daum